Waldemar Leibhahn: Gründer, Geschäftsführer & Produktentwickler
Waldemar gründete die LFS Organic Polymer GmbH & Co. KG als Ort für die Entwicklung, Produktion und den Vertrieb von innovativen Epoxidharz-Beschichtungen. Dabei verfolgt er stets das Ziel, CO2 zu reduzieren und biobasierte Produkte auf den Markt zu bringen.
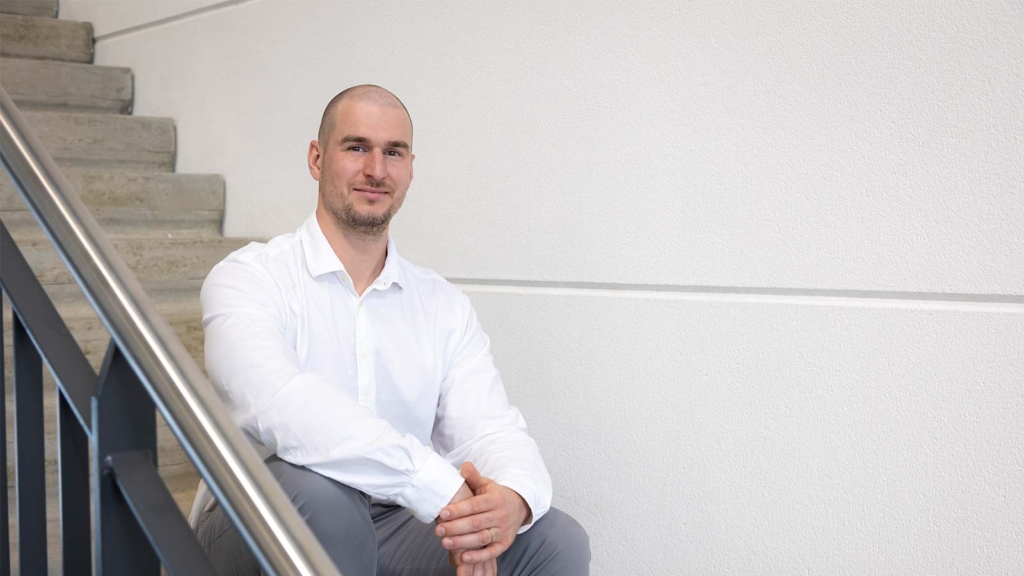
- Waldemar, was hat dich in die Welt der Chemie gebracht?
- Du hast Erfahrung in vielen Bereichen, was ist dein „Steckenpferd“?
- Warum hast du dich selbstständig gemacht und ORGANIC POLYMER gegründet?
- Welchen Herausforderungen hast du dich seit der Gründung gestellt?
- Was ist deine Vision?
- Was ist so besonders an deinen Produkten?
- Woran arbeitest du zurzeit in der Produktentwicklung?
- Welche Trends siehst du in der Branche?
- Welche Pläne hast du für ORGANIC POYLMER?
Waldemar, was hat dich in die Welt der Chemie gebracht?
Der Klassiker: mein Vater. Er arbeitete bei einem bekannten Kunstharz-Hersteller in meinem Heimatort Aurich und besorgte mir einen Nebenjob in der Produktion – damals war ich ein Teenager. Was mit einem klassischen Nebenjob begann, führte mich in eine Ausbildung zum Chemielaboranten. Diese schloss ich mit Auszeichnung ab. Danach sammelte ich Berufserfahrung sowohl bei der ABP-Chemie (AB-Polymerchemie GmbH) als auch bei der Hobum (Hobum Oleochemicals GmbH).
Mein tiefes Verständnis für die Anwendung von Beschichtungen, Lacken und Klebern erarbeitete ich mir in vielen Projekten. Ich entwickelte und modifizierte diverse Produkte, begleitete deren Produktion und sicherte die Qualität bis zur Marktreife und darüber hinaus. „Ob in der Entwicklung oder in der Qualitätskontrolle – an vielen Beschichtungen, Bindemitteln, Klebern und Lacken, die heute meine ehemaligen Arbeitgeber verkaufen, war ich beteiligt.“
Du hast Erfahrung in vielen Bereichen, was ist dein „Steckenpferd“?
Meine Leidenschaft ist klar das Entwickeln von Produkten. Da liegt meine Stärke. Allerdings verdient die Anwendungstechnik meinen größten Respekt. Im Rahmen von Qualitätskontrollen, durfte ich Testflächen beschichten. Daher weiß ich, dass die verarbeitenden Unternehmen nicht nur einen Knochenjob machen, sondern viel Wissen mitbringen müssen. Von außen erscheint das Verlegen von Epoxidharzbeschichtungen nämlich simple. Ist es aber nicht. Zum einen müssen Verarbeiter genau wissen, was sie tun. Harz, Härten, Zusatzstoffe – alles muss korrekt vermengt werden. Andernfalls besteht das Risiko, dass das Harz nicht aushärtet, milchig wird oder dass es zu stark erhitzt, bis hin zu Rauchentwicklung. Zum anderen ist jeder Untergrund sowie das Umgebungsklima anders und es sind viele Fragen im Vorfeld zu klären.
Dann kommt das eigentliche Verlegen, was zugig und akkurat ablaufen muss. Epoxidharz verzeiht zwar Fehler, aber auch nicht jeden.
Warum hast du dich selbstständig gemacht und ORGANIC POLYMER gegründet?
Es klingt zwar etwas hochtragend, aber dennoch: Ich weiß, wie und aus welchen Rohstoffen herkömmliche Epoxidharz-Produkte hergestellt werden. Ich verstehe die Tragweite für unsere Umwelt und die Menschen, die mit den Produkten arbeiten und leben. Ich weiß, dass es anders und besser geht. Ich war es leid, vertröstet zu werden und nach dem Motto „Wir machen alles wie immer.“ zu arbeiten. Also habe ich mich entschieden, die Komfortzone zu verlassen und ORGANIC POLYMER zu gründen. Ein Unternehmen, das eine bessere Alternative bietet. Und das in jeglicher Hinsicht.
Welchen Herausforderungen hast du dich seit der Gründung gestellt?
Die erst Herausforderung war eine biobasierte Alternative zu petrochemischen Epoxidharzbeschichtung zu entwickeln. Das habe ich bereits vor der Gründung geschafft.
Danach kam die Investorensuche. Denn ohne fremdes Startkapital wäre es mir nicht möglich gewesen, eine Produktion aufzubauen. Eine passende Immobilie zu finden, war auch schwer und hat mich viel Zeit und Geduld gekostet. Der Immobilienmarkt in Hamburg ist ein hartes Pflaster, auch für gewerbliche Objekte.
Was für mich doch die größte Herausforderung war und ist, sind die bürokratischen Hürden. Aus meiner Sicht ist Deutschland nicht besonders Gründer-freundlich – beginnend bei Vorauszahlungen von Steuern, bis hin zu undurchsichtigen Zertifizierungsprozessen und -richtlinien.
Die Herausforderungen enden nicht – ich stelle mich ihnen aber gern!
Was ist deine Vision?
Ich will in der Bauchemie-Branche den Stand der Dinge verändern. Ich will Verarbeitern und Nutzenden die Chance geben, sich für umweltbewusste, gesundheitlich verträgliche Bodenbeschichtungen entscheiden zu können. Ich will Produkte auf den Markt bringen, die zu 100% biobasiert sind.
Was ist so besonders an deinen Produkten?
Abgesehen davon, dass sie einmalig auf dem Markt sind?
Die chemischen Besonderheiten unserer Beschichtungssystems aus Epoxidharz sind vielfältig.
- Es ist zu 87% biobasiert – wir arbeiten daran, den Anteil zu steigern.
- Es ist frei von ökotoxischen Stoffen.
- Es ist frei von BPA- und BPA-Derivaten, Salicylsäure, Kohlenwasserstoffharz, styrolisiertem Phenol und Benzylalkohol.
- Es ist frei von VOC.
- Es besteht aus nachwachsenden und recycelten Rohstoffen.
Doch viele wichtiger finde ich den Nutzen der verarbeitenden Unternehmen. Denn sie sparen sich viel Arbeit. In manchen Projekten entfiel das ansträngende Kugelstrahlen des Untergrundes und doppeltes Grundieren. Denn der OP-Primer 001 kann auf verölten und nassen Oberflächen eingesetzt werden. Klingt unglaublich, ist aber wahr.
Außerdem entfallen lästige Wartezeit: die Grundierung ist nach 3 Stunden überbeschichtbar und das Zwei-Schichten-System kann bereits nach 8 Stunden leicht belastet werden. Das freut auch den Kunden.
Beim Transport gehen Verarbeiter kein Risiko durch Gefahrgut ein – unsere Produkte sind nämlich kein Gefahrgut.
Außerdem ist aus meiner Sicht ist der Geruch ein Benefit. Es ist zwar etwas, woran sich Verarbeiter gewöhnt haben. Dennoch, ohne Kopfschmerzen in den Feierabend zu starten, kann nicht verkehrt sein.
Und wenn wir schon bei der Gesundheit sind. Unsere Produkte haben ein gesenktes Kontaktallergie-Risiko und wenige bis keine gesundheitlichen Risiken. Was in Anbetracht von Arbeitsunfähigkeiten aufgrund von berufsbedingten Allergien auf alle Fälle ein großer Vorteil ist – für den Verarbeiter und das Unternehmen.
Woran arbeitest du zurzeit in der Produktentwicklung?
Das ist ein Geheimnis 😉 So viel kann ich aber verraten: es ist eine biobasierte Beschichtung für Anwendungsfälle, die wir mit OP-Primer 001 und OP-Coat 100 noch nicht abdecken.
Welche Trends siehst du in der Branche?
Nach dem seit über 50 Jahren die Produkte auf Basis fast derselben Rohstoffe und Rezepturen hergestellt werden, kommt der „grüne Wandel“ langsam, aber sicher auch in der Bauchemie an. Allerdings beobachte ich, dass viel Greenwashing betrieben wird. Es werden schwammige Formulierungen benutzt, Produkte als „natürlich“ angepriesen und mit selbstgebauten Siegeln geworben. Werfe ich jedoch einen Blick in die Sicherheitsdatenblätter bzw. technischen Informationen, finde ich wenig „Natürliches“ oder „Umweltfreundliches“. Wenn auf Produkten die Gefahrensymbole „Ernste Gesundheitsgefahr“ und „Umweltgefährlich“ klebt, sollten die Hersteller die Verarbeiter und Endverbraucher nicht für blauäugig verkaufen.
Aber ich sehe eine positive Entwicklung hin zur mehr Bewusstsein für die Umwelt und Gesundheit – angetrieben von den Endverbrauchen und gesetzlichen Regulierungen.
Welche Pläne hast du für ORGANIC POYLMER?
Im Bereich F&E bin ich an neuen Produkten dran. Dabei will ich den Bio-Kohlenstoffanteil weiter nach oben treiben. Außerdem stehen wir in Verhandlung mit Unternehmen. Wir wollen Kooperationen außerhalb unseres Kerngeschäfts eingehen. Dazu zu einem späteren Zeitpunkt mehr.
Das Team wird wachsen. In absehbarer Zeit brauchen wir Unterstützung an allen Bereichen, aber in erster Linie in der Produktion.
Außerdem sind wir weiterhin auf der Suche nach attraktiven, herausfordernden Projekten. Bei ORGANIC POLYMER bleibt es interessant.
Neugierig geworden?
Dann lernen Sie unsere Produkte kennen – im Gespräch, als Muster oder direkt im Projekt.